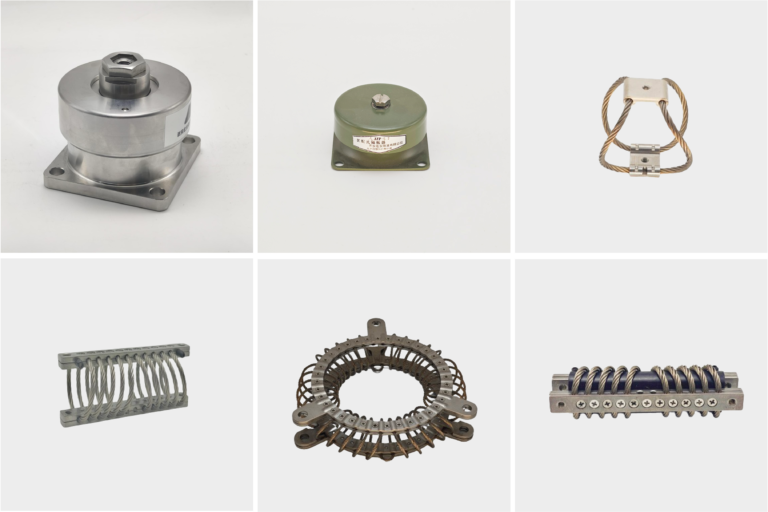
Table of Contents
What is a Vibration Isolator?
A vibration isolator is a specialized device designed to reduce the transmission of vibrations from machinery to its surroundings. These isolators are placed between vibrating equipment—such as HVAC systems, industrial machines, or precision instruments—and their supporting structures. By absorbing and dampening vibrational energy, they reduce noise, prevent structural damage, and extend equipment lifespan.
Whether addressing low-frequency disturbances or high-intensity vibrations, isolators are engineered to meet specific performance criteria. Advanced designs, like spring mounts, and wire rope isolators, ensure precise isolation for various industrial needs. Selecting the right isolator enhances operational reliability, minimizes downtime, and ensures compliance with noise and vibration standards.
How Does It Work?
Have you ever felt the floor rumble when heavy machinery is running? That’s where vibration isolators come into play. These devices absorb vibration energy and turn it into harmless heat, keeping both your equipment and surroundings safe. Whether made from rubber, springs, or wire ropes, isolators sit between vibrating sources and what needs protection. They don’t just dampen the vibrations—they stop resonance from amplifying them, which is crucial for long-term durability. It’s a simple solution to a noisy, vibrating problem!
Why is Vibration Isolation Important in Industrial Applications?
Imagine your machinery running smoother, quieter, and lasting longer—sounds ideal, right? In my line of work, I’ve seen how effective vibration isolation can turn this into a reality. It’s not just about noise reduction; it’s about preventing costly damage and extending the life of your equipment. Constant vibrations wear down machinery, leading to expensive maintenance and unscheduled downtime. With the right isolation, you’ll not only stay compliant with regulations but also keep your operations efficient and hassle-free.
What Materials Are Commonly Used in the Manufacturing of Vibration Isolators?
- Rubber: Natural or synthetic rubber is used for its flexibility and ability to absorb vibrations across a wide range of frequencies.
- Stainless Steel: Often found in wire rope isolators, stainless steel is highly durable and resistant to corrosion, making it ideal for extreme environments.
- Neoprene: A synthetic rubber used for its high resistance to oil, chemicals, and weathering.
- Springs: Steel or alloy springs are commonly used for heavy-duty vibration control where both shock absorption and vibration isolation are required.
What Are the Different Types of Vibration Isolators Available?
When it comes to vibration isolation, selecting the right type of isolator is key to ensuring optimal performance. Here are several types of vibration isolators, each designed for specific applications and environmental conditions. Common types include:
Material | Properties | Applications |
---|---|---|
Natural Rubber | High elasticity and excellent vibration damping; susceptible to aging and environmental degradation. | General-purpose isolators in machinery and automotive industries. |
Synthetic Rubber (e.g., Neoprene) | Resistant to oil, chemicals, and weathering; maintains flexibility over a wide temperature range. | HVAC systems, marine applications, and environments exposed to oils and chemicals. |
Stainless Steel | High strength, corrosion resistance, and durability; lacks inherent damping properties. | Wire rope isolators, heavy machinery, and environments with extreme temperatures or corrosive elements. |
Springs (Steel or Alloy) | Provides load-bearing capacity and flexibility; requires additional damping mechanisms to control resonance. | Heavy-duty vibration control in industrial equipment and structures. |
How Do Vibration Isolators Reduce Noise and Equipment Damage?
One thing I’ve learned over the years is just how effective vibration isolators are at reducing both noise and equipment damage. When machinery runs, it generates vibrations that can travel through structures, creating sound waves that amplify noise. This can be a real issue, especially in industrial settings. Vibration isolators help by physically dampening these vibrations, reducing the spread of sound and creating a quieter work environment.
But the benefits go beyond just noise control. Isolators also protect mechanical parts by limiting excessive movement, which can cause parts to misalign or even lead to failure. This kind of stress on equipment can result in costly repairs or downtime. By keeping vibrations in check, isolators help extend the life of machinery and keep everything running smoothly for the long haul.
What Industries Rely on Vibration Isolators for Operational Efficiency?
When you look at the industries that depend on vibration isolators, it’s clear how essential they are for maintaining operational efficiency. Let me walk you through a few key sectors where these solutions make a huge difference:
Industry | Key Role of Vibration Isolators |
---|---|
Manufacturing | Keeps precision equipment running smoothly, preventing wear and tear, ensuring longevity, and maintaining production consistency. |
Aerospace and Defense | Safeguards avionics and navigation systems from vibrations, ensuring reliability in high-stakes environments. |
HVAC | Reduces vibration and noise in large systems, enabling quieter, more efficient operation for commercial and residential applications. |
Automotive and Rail | Enhances ride comfort, reduces wear, and extends the lifespan of vehicles in both automotive and rail sectors. |
Medical Equipment | Eliminates vibrations in sensitive devices like MRI machines, ensuring accuracy and uninterrupted critical medical procedures. |
In each of these fields, reliable vibration isolation isn’t just a nice-to-have—it. It’s essential for keeping operations running efficiently and protecting valuable equipment.
How Do You Select the Right Vibration Isolator for Specific Equipment?
Choosing the right vibration isolator can feel like solving a puzzle—get one piece wrong, and the whole system can falter. I’ve seen companies overlook key factors, only to deal with unnecessary downtime and equipment wear. To help avoid those costly mistakes, here’s what you need to keep in mind when selecting the perfect isolator:
Load Capacity: Make sure the isolator can bear the equipment’s weight. If it’s undersized, you won’t get the performance you need, and your machinery may suffer for it.
Vibration Frequency: Matching the machine’s operational frequency with the isolator’s natural frequency is essential. This is where you’ll see the best vibration damping.
Environmental Conditions: Whether your equipment is operating in extreme temperatures, wet conditions, or exposed to chemicals, the right isolator material can make or break its performance.
Mounting Configuration: Not every isolator goes under a machine. Some setups require more complex solutions, like ceiling or wall mounts, where anti-vibration systems come into play.
Customization: Sometimes, the only solution is custom design, especially when dealing with space restrictions or unusual vibration patterns.
Consulting with an expert on vibration isolation is always a smart move to ensure that the isolator fits your equipment and operational needs perfectly.
What is the Difference Between Passive and Active Vibration Isolation?
If you’ve ever wondered why some industries use passive vibration isolation while others lean toward active systems, it all comes down to how these systems manage vibrations. Let me break it down:
Passive Vibration Isolation: This method is all about simplicity. Using materials like springs, rubber, or wire ropes, passive isolators absorb and dissipate vibrations through physical means. They’re cost-effective, low-maintenance, and perfect for most everyday applications. I often recommend them for setups that don’t require extreme precision but still need reliable performance.
Active Vibration Isolation: Now, if you’re dealing with environments where even the slightest vibration could throw off sensitive equipment—think laboratory tools or aerospace systems—active isolation is the way to go. These systems use electronic sensors and actuators to detect and counteract vibrations in real-time. Yes, they come with a higher price tag, but the level of control they offer is unmatched.
So, which is better? It depends on your needs. For general use, passive systems do the job well. But when precision is key, active vibration isolation steps up as the superior option.
Conclusion
Vibration isolation is essential for protecting machinery, reducing noise, and ensuring operational efficiency across various industries. Proper isolator selection improves equipment performance, prevents costly downtime, and enhances overall productivity.